Extrusion Plant
It consists of 2 units of 1.650 mt extrusion lines and 1 unit: 2.200 mt of extrusion lines.
Its annual total capacity is 17.000 tons on average. The facility, which can use tickets (aluminum round billet used as raw material) from 100nnm to 203mm in diameter, can respond to a wide usage area that may be needed in terms of aluminum profile.
The raw materials used have extremely close chemical composition and physical properties;
6063 AA USA, 6060 ETIAL TURKIYE, AlMgSi0.5 DIN GERMANY alloys.
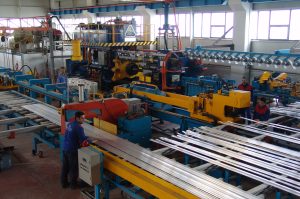
The profiles coming out of the extrusion press are cooled quickly with water or air cooling system, cold stretching is performed and cut to the requested length. Afterwards, the profiles are hardened by applying artificial aging heat treatment (thermal) according to the characteristics of the order.
Satination Unit
It is used to give a mechanical satin look on the aluminum profile surface. Both the lower and upper surfaces of the profiles can be satinized at the same time. Since the residence time of the aluminum profiles satined in this way in the caustic bath during the anodizing process is extremely shortened, the satin matte anodized appearance is obtained more easily and in a high quality manner.
All profiles are also applied before the electrostatic powder coating process, within the framework of high quality standards, as it can eliminate some surface defects that may arise from the extrusion process, increase the paint life and quality due to better adhesion of the powder paint!
Polishing Unit
In order to polish the surface of the profiles, brushes made of special cloths are applied to the surface with a special polish and polishing is done. If there are lines or some surface defects on the surface that may be caused by the extrusion process, the lines are removed with a special sisal brush or belt sanding before polishing, and then polishing is done.
Electrostatic Powder Coating Plant
In the electrostatic powder coating facility, paint coating process is carried out in accordance with Qualicoat specifications in all desired RAL colors in line with the demands of the customers. Paint coated profiles gain resistance against water, temperature changes, humidity, corrosion and harmful UV rays of the sun.
Paint coated profiles have a coating thickness between 60 and 80 microns and are guaranteed for 20 years, excluding assembly or usage errors.
In the facility, paint coating can be made up to a maximum thickness of 250 microns, and profiles with a maximum length of 7 meters can be painted.
The annual total dyeing capacity is approximately 12.000 tons. Profiles are passed through a total of 4 stages in the dyeing process.
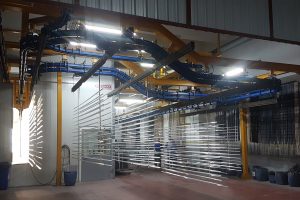
In the first stage, a much better paint adhesion surface is obtained by passing the profiles through the satination unit. In this process, it increases the life and quality of the paint layer positively and significantly.
In the second stage, the profiles are immersed in degreasing, caustic and neutralization baths, and finally, they are dried in the drying oven by chromating. Thus, it becomes ready to be painted.
The quality of the pre-treatment applied to the surface before painting is one of the most important factors affecting the life and quality of the paint layer. Even if the paint layer is damaged for any reason, the risk of corrosion is less and ineffective in profiles that have undergone a good surface pre-treatment!
In the third stage, the paint, which passes through the gun and is charged with static electricity, homogeneously by means of robots with electrostatic corona system Gema brand guns on the profiles, is sprayed onto the electrically grounded profiles in the cabin, and the desired paint coating thickness is adjusted.
In the fourth and final stage, the profiles passing through the cabin enter the baking oven with the conveyor system. It is kept at the recommended temperature for a certain period of time according to the type of paint. In the meantime, the powder paint melts, covers the surface, wraps and acquires a decorative appearance in a bright preferred color.
Anodizing Plant
Anodizing facility, which started production as of October 2007, is new and modern, as well as equipped with state-of-the-art automatic control systems. In this way, there is no problem in obtaining the coating thickness and color tones demanded by the customers and ensuring the standard and continuity of these obtained color tones. In addition, controls and tests are carried out at every stage of production by the Quality Control Department and in its own laboratory. In accordance with Qualanod specifications, all kinds of anodized coatings can be made on demand, from natural, white and black, yellow and shades, light bronze to dark brown tones with matte, semi-matt and glossy properties in different surface effects. Anodized coating thickness is between 12 and 14 microns, and it is guaranteed for 30 years, excluding assembly or usage errors. In the facility, anodized coating can be made up to a maximum thickness of 30 microns, and profiles with a maximum length of 6.5 meters can be anodized. The annual total anodized coating capacity is 9.600 tons on average (6.750.000 m2).
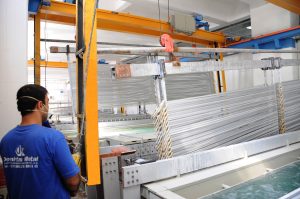
Mold Manufacturing Workshop
It produces molds for the extrusion lines in order to produce the general or custom profiles requested by the customers. In this way, it is able to respond to the demands of its customers in the shortest, high quality and sensitive manner. Experienced, trained and equipped technical team, continuous and innovative R&D studies, computer-aided technology High Speed C.N.C. The machining center serves customers with its always erosion, manual drill, lathe, milling and pantograph benches, a wide variety of equipment and a capacity of 1,000 molds per year. Profiles to be molded; It is examined by the design and construction team and its manufacturability is decided, the mold dimensions are calculated and the drawings are made in the CAD environment and submitted to the customer’s approval.
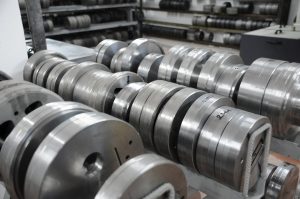
After receiving customer approval, mold, manufacturing, design studies and production planning are done. According to the calculated mold dimensions, the certified steel product is cut and production begins. The mold, which is processed precisely and meticulously to the smallest detail by our experienced and trained technical staff, is sent to experienced and certified companies and heat treated.
At the last stage, trials and tests are made on the extrusion lines of the heart, and if necessary, corrections are made and the profile is presented to the production and orders of the customers in the dimensions and tolerances requested by the customers.
A well-designed mold, providing superior surface quality in profile production, ensuring desired tolerances, affects performance, standardity, anodized and electrostatic powder paint coating quality positively and significantly!
Protective Film Coating Unit
Profiles are covered with a special protective film after passing the final quality control tests in order to ensure that the profiles are not scratched, not worn out in case of shipment and processing, and remain as clean as the day they were first produced, in line with the wishes and orders of the customers.
Packaging Units
After passing the final quality control tests and covering with a protective film, the profiles are packed in kraft paper or nylon with the requested specifications. It is carefully kept in our warehouse until the delivery period. If requested, the profiles can be placed in wooden crates, pallets, etc. Packed with packaging methods and stored or shipped in desired specifications!