Extrusionsanlage
Es besteht aus 2 Einheiten mit 1.650 mt Extrusionslinien und 1 Einheit mit 2.200 mt Extrusionslinien.
Die jährliche Gesamtkapazität beträgt durchschnittlich 17.000 Tonnen. Die Anlage, die Tickets (Rundknüppel aus Aluminium, die als Rohmaterial verwendet werden) mit einem Durchmesser von 100 nm bis 203 mm verwenden kann, kann auf einen breiten Anwendungsbereich reagieren, der möglicherweise in Bezug auf Aluminiumprofile benötigt wird.
Die verwendeten Rohstoffe haben eine sehr ähnliche chemische Zusammensetzung und physikalische Eigenschaften;
6063 AA USA, 6060 ETIAL TURKIYE, AlMgSi0,5 DIN DEUTSCHLAND Legierungen.
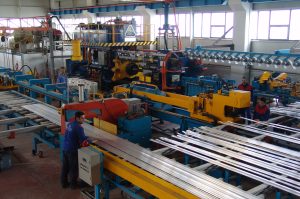
Die aus der Strangpresse kommenden Profile werden schnell mit einem Wasser- oder Luftkühlsystem abgekühlt, kalt gereckt und auf die gewünschte Länge geschnitten. Anschließend werden die Profile durch Warmauslagerung (thermisch) entsprechend den Auftragseigenschaften gehärtet.
Satiniereinheit
Es wird verwendet, um der Oberfläche von Aluminiumprofilen ein mechanisch satiniertes Aussehen zu verleihen. Sowohl die Unter- als auch die Oberseite der Profile können gleichzeitig satiniert werden. Da die Verweilzeit der so satinierten Aluminiumprofile im Laugenbad während des Eloxalprozesses extrem verkürzt wird, wird die seidenmatte Eloxaloptik leichter und hochwertiger erreicht.
Alle Profile werden auch vor dem elektrostatischen Pulverbeschichtungsprozess im Rahmen hoher Qualitätsstandards aufgebracht, da dadurch einige Oberflächenfehler beseitigt werden können, die durch den Extrusionsprozess entstehen können, die Lacklebensdauer und -qualität durch bessere Haftung des Pulverlacks erhöht werden!
Poliereinheit
Um die Oberfläche der Profile zu polieren, werden Bürsten aus speziellen Tüchern mit einer speziellen Politur auf die Oberfläche aufgebracht und poliert. Wenn Linien oder einige Oberflächenfehler auf der Oberfläche vorhanden sind, die durch den Extrusionsprozess verursacht werden können, werden die Linien vor dem Polieren mit einer speziellen Sisalbürste oder einem Bandschleifen entfernt, und dann wird poliert.
Elektrostatische Pulverbeschichtungsanlage
In der elektrostatischen Pulverbeschichtungsanlage erfolgt die Lackierung nach Qualicoat-Vorgabe in allen gewünschten RAL-Farben nach Kundenwunsch. Lackierte Profile werden widerstandsfähiger gegen Wasser, Temperaturschwankungen, Feuchtigkeit, Korrosion und schädliche UV-Strahlen der Sonne.
Lackierte Profile haben eine Schichtdicke zwischen 60 und 80 Mikron und haben eine Garantie von 20 Jahren, ausgenommen Montage- oder Gebrauchsfehler.
In der Anlage können Farbbeschichtungen bis zu einer maximalen Dicke von 250 Mikron durchgeführt und Profile mit einer maximalen Länge von 7 Metern lackiert werden.
Die jährliche Gesamtfärbekapazität beträgt ca. 12.000 Tonnen. Profile durchlaufen im Färbeprozess insgesamt 4 Stufen.
Yıllık toplam boyama kapasitesi ortalama 12.000 ton’dur. Boyama prosesinde profiller toplam 4 aşamadan geçirilir.
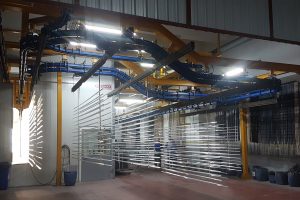
In der ersten Stufe wird eine deutlich bessere Lackhaftungsoberfläche erzielt, indem die Profile durch die Satiniereinheit geführt werden. Dabei erhöht es die Lebensdauer und Qualität der Lackschicht positiv und deutlich.
In der zweiten Stufe werden die Profile in Entfettungs-, Laugen- und Neutralisationsbäder getaucht und abschließend im Trockenschrank durch Chromatieren getrocknet. So wird es fertig zum Lackieren.
Die Qualität der Vorbehandlung, die vor dem Lackieren auf die Oberfläche aufgetragen wird, ist einer der wichtigsten Faktoren, die die Lebensdauer und Qualität der Farbschicht beeinflussen. Selbst wenn die Lackschicht aus irgendeinem Grund beschädigt ist, ist die Korrosionsgefahr bei Profilen, die eine gute Oberflächenvorbehandlung erfahren haben, geringer und wirkungslos!
In der dritten Stufe wird der Lack, der durch die Pistole läuft und statisch aufgeladen wird, mittels Robotern mit elektrostatischem Koronasystem Pistolen der Marke Gema homogen auf die Profile auf die elektrisch geerdeten Profile in der Kabine gesprüht und das gewünschte Lackschichtdicke angepasst.
In der vierten und letzten Stufe gelangen die durch die Kabine laufenden Profile mit dem Fördersystem in den Backofen. Je nach Art der Farbe wird es für eine bestimmte Zeit auf der empfohlenen Temperatur gehalten. Währenddessen schmilzt der Pulverlack, bedeckt die Oberfläche, umhüllt und erhält ein dekoratives Aussehen in einer hellen Vorzugsfarbe.
Anodisierungsanlage
Die Eloxalanlage, die im Oktober 2007 die Produktion aufgenommen hat, ist neu und modern und mit modernsten automatischen Steuerungssystemen ausgestattet. Auf diese Weise ist es kein Problem, die von den Kunden geforderten Beschichtungsdicken und Farbtöne zu erhalten und den Standard und die Kontinuität dieser erhaltenen Farbtöne sicherzustellen. Darüber hinaus werden in jeder Phase der Produktion Kontrollen und Tests durch die Abteilung Qualitätskontrolle und im eigenen Labor durchgeführt. Gemäß den Qualanod-Spezifikationen können alle Arten von Eloxalbeschichtungen auf Anfrage hergestellt werden, von Natur, Weiß und Schwarz, Gelb und Schattierungen, Hellbronze bis zu dunklen Brauntönen mit matten, halbmatten und glänzenden Eigenschaften in verschiedenen Oberflächeneffekten. Die Dicke der Eloxalschicht liegt zwischen 12 und 14 Mikron und hat eine Garantie von 30 Jahren, ausgenommen Montage- oder Gebrauchsfehler. In der Anlage können Eloxalschichten bis zu einer maximalen Dicke von 30 Mikron hergestellt und Profile mit einer maximalen Länge von 6,5 Metern eloxiert werden. Die jährliche Gesamtkapazität für Eloxalbeschichtung beträgt durchschnittlich 9.600 Tonnen (6.750.000 m2).
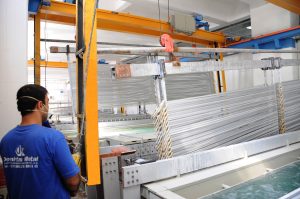
Formenbau-Werkstatt
Es produziert Formen für die Extrusionslinien, um die von den Kunden gewünschten allgemeinen oder kundenspezifischen Profile herzustellen. Auf diese Weise ist es in der Lage, auf die Anforderungen seiner Kunden in kürzester, qualitativ hochwertiger und sensibler Weise zu reagieren. Erfahrenes, geschultes und ausgestattetes technisches Team, kontinuierliche und innovative Forschungs- und Entwicklungsstudien, computergestützte Technologie High Speed C.N.C. Das Bearbeitungszentrum dient Kunden mit seinen ständigen Erodier-, Handbohr-, Dreh-, Fräs- und Stromabnehmerbänken, einer großen Vielfalt an Geräten und einer Kapazität von 1.000 Formen pro Jahr. Es wird vom Design- und Konstruktionsteam geprüft und auf Herstellbarkeit entschieden, die Formabmessungen berechnet und die Zeichnungen in der CAD-Umgebung erstellt und dem Kunden zur Freigabe vorgelegt.
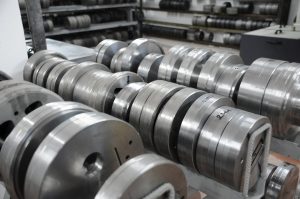
Nach Erhalt der Kundenfreigabe werden Form, Fertigung, Designstudien und Produktionsplanung durchgeführt. Gemäß den berechneten Formabmessungen wird das zertifizierte Stahlprodukt geschnitten und die Produktion beginnt. Die von unserem erfahrenen und geschulten Fachpersonal bis ins kleinste Detail präzise und akribisch bearbeitete Form wird an erfahrene und zertifizierte Betriebe versandt und wärmebehandelt.
In der letzten Phase werden an den Extrusionslinien des Herzens Versuche und Tests durchgeführt, gegebenenfalls Korrekturen vorgenommen und das Profil in den von den Kunden gewünschten Abmessungen und Toleranzen der Produktion und den Bestellungen der Kunden vorgelegt.
Eine gut konstruierte Form, die eine hervorragende Oberflächenqualität bei der Profilherstellung bietet und die gewünschten Toleranzen sicherstellt, wirkt sich positiv und signifikant auf Leistung, Standardität, Eloxal- und elektrostatische Pulverlackbeschichtung aus!
Schutzfilm-Beschichtungsanlage
Die Profile werden nach bestandener abschließender Qualitätskontrolle mit einer speziellen Schutzfolie überzogen, um sicherzustellen, dass die Profile nicht zerkratzt, beim Versand und bei der Verarbeitung nicht abgenutzt werden und so sauber bleiben wie am Tag ihrer ersten Produktion in der Linie mit den Wünschen und Aufträgen der Kunden.
Verpackungseinheiten
Nach dem Bestehen der abschließenden Qualitätskontrollen und dem Abdecken mit einer Schutzfolie werden die Profile in Kraftpapier oder Nylon mit den gewünschten Spezifikationen verpackt. Es wird bis zum Liefertermin sorgfältig in unserem Lager verwahrt, auf Wunsch können die Profile in Holzkisten, Paletten etc. Mit Verpackungsmethoden verpackt und in den gewünschten Spezifikationen gelagert oder versendet!